Calibração De Válvulas: Precisão Garantida
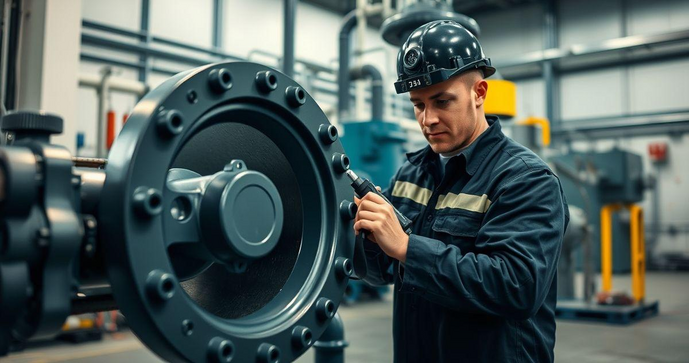
Por: Lucas - 01 de Julho de 2025
A calibração de válvulas é um processo crucial para garantir a eficiência e a precisão em sistemas industriais. Com o tempo, as válvulas podem apresentar desvios em seu funcionamento, o que pode comprometer a performance de todo o sistema. Neste artigo, abordaremos a importância da calibração de válvulas, o passo a passo para realizá-la corretamente, os erros comuns a serem evitados e a necessidade de manutenção regular para assegurar o desempenho ideal das válvulas.
Importância da Calibração de Válvulas para a Eficiência Operacional
A calibração de válvulas é um aspecto fundamental na operação de sistemas industriais, pois garante que os equipamentos funcionem de maneira eficiente e segura. As válvulas desempenham um papel crucial no controle do fluxo de fluidos, e qualquer desvio em seu funcionamento pode resultar em perdas significativas de eficiência, aumento de custos operacionais e até mesmo riscos à segurança. Neste contexto, entender a importância da calibração de válvulas é essencial para manter a integridade e a eficácia dos processos industriais.
Um dos principais motivos para a calibração de válvulas é a manutenção da precisão no controle de fluxo. Válvulas descalibradas podem levar a um fluxo excessivo ou insuficiente de fluidos, o que pode comprometer a qualidade do produto final. Por exemplo, em processos químicos, a dosagem precisa de reagentes é vital para garantir a reação desejada. Se uma válvula não estiver calibrada corretamente, pode resultar em uma mistura inadequada, afetando a qualidade do produto e gerando desperdícios.
Além disso, a calibração de válvulas contribui para a eficiência energética dos sistemas. Válvulas que não operam em suas especificações ideais podem causar um aumento no consumo de energia, uma vez que as bombas e outros equipamentos precisam trabalhar mais para compensar a perda de eficiência. Isso não apenas eleva os custos operacionais, mas também pode resultar em um impacto ambiental negativo devido ao aumento das emissões de carbono. Portanto, a calibração regular das válvulas é uma prática recomendada para otimizar o consumo de energia e reduzir a pegada ambiental da operação.
Outro aspecto importante a ser considerado é a segurança operacional. Válvulas descalibradas podem levar a situações perigosas, como vazamentos ou falhas no sistema. Em indústrias que lidam com substâncias químicas perigosas ou pressões elevadas, a integridade das válvulas é crucial para evitar acidentes. A calibração regular ajuda a identificar problemas antes que se tornem críticos, garantindo que as válvulas funcionem corretamente e que os sistemas operem dentro dos limites de segurança estabelecidos.
Além disso, a calibração de válvulas pode prolongar a vida útil dos equipamentos. Válvulas que operam fora de suas especificações podem sofrer desgaste prematuro, resultando em falhas e a necessidade de substituições frequentes. Ao garantir que as válvulas estejam calibradas corretamente, as empresas podem reduzir os custos de manutenção e substituição, aumentando a confiabilidade do sistema como um todo.
É importante ressaltar que a calibração de válvulas deve ser realizada por profissionais qualificados, que possuam conhecimento técnico e experiência na área. O processo envolve a verificação e ajuste das configurações da válvula, utilizando equipamentos de medição apropriados. A calibração deve ser realizada em intervalos regulares, de acordo com as recomendações do fabricante e as condições de operação do sistema.
Além disso, a implementação de um programa de manutenção preventiva que inclua a calibração de válvulas pode trazer benefícios significativos para a operação. Isso não apenas ajuda a garantir que as válvulas estejam sempre em condições ideais de funcionamento, mas também permite que as empresas identifiquem e resolvam problemas antes que eles afetem a produção. Um programa de manutenção bem estruturado pode resultar em uma operação mais eficiente, segura e econômica.
Por fim, a calibração de válvulas é um investimento que traz retornos significativos em termos de eficiência operacional, segurança e redução de custos. Empresas que priorizam a calibração regular de suas válvulas estão mais bem posicionadas para enfrentar os desafios do mercado e garantir a qualidade de seus produtos. Se você está em busca de soluções para otimizar o controle de fluxo em seu sistema, considere a Válvula solenoide para água , que pode ser uma excelente opção para aplicações que exigem precisão e confiabilidade.
Em resumo, a calibração de válvulas é um componente essencial para a eficiência operacional em ambientes industriais. Ao garantir que as válvulas estejam funcionando corretamente, as empresas podem melhorar a qualidade do produto, reduzir custos operacionais e aumentar a segurança em suas operações. Portanto, investir na calibração de válvulas é uma decisão estratégica que pode trazer benefícios duradouros para qualquer organização.
Passo a Passo para Realizar a Calibração de Válvulas
A calibração de válvulas é um processo essencial para garantir que os sistemas industriais operem de maneira eficiente e segura. A seguir, apresentamos um guia passo a passo para realizar a calibração de válvulas, abordando desde a preparação até a verificação final. Este procedimento deve ser realizado por profissionais qualificados, que possuam conhecimento técnico e experiência na área.
1. Preparação e Planejamento
Antes de iniciar o processo de calibração, é fundamental realizar um planejamento adequado. Isso inclui a identificação da válvula a ser calibrada, a coleta de informações sobre suas especificações e a definição dos instrumentos de medição que serão utilizados. É importante ter em mãos o manual do fabricante, que pode fornecer orientações específicas sobre a calibração da válvula em questão.
Além disso, é necessário garantir que todas as ferramentas e equipamentos estejam disponíveis e em boas condições de funcionamento. Isso pode incluir manômetros, calibradores, chaves de fenda, entre outros. A segurança também deve ser uma prioridade; portanto, certifique-se de que todos os profissionais envolvidos estejam utilizando os Equipamentos de Proteção Individual (EPIs) adequados.
2. Desconexão do Sistema
Antes de realizar a calibração, é essencial desconectar a válvula do sistema. Isso pode envolver o fechamento de válvulas de isolamento e a drenagem de fluidos que possam estar presentes na linha. A desconexão é crucial para evitar acidentes e garantir que a calibração seja realizada em um ambiente seguro. Após a desconexão, verifique se não há pressão residual na válvula.
3. Inspeção Visual
Uma vez que a válvula esteja desconectada, realize uma inspeção visual detalhada. Verifique se há sinais de desgaste, corrosão ou danos. Inspecione as juntas, selos e outros componentes para garantir que estejam em boas condições. Se forem identificados problemas, é recomendável realizar os reparos necessários antes de prosseguir com a calibração.
4. Conexão do Equipamento de Medição
Após a inspeção, conecte os instrumentos de medição à válvula. Isso pode incluir manômetros ou calibradores que permitirão monitorar a pressão e o fluxo durante o processo de calibração. Certifique-se de que as conexões estejam firmes e seguras para evitar vazamentos. É importante seguir as instruções do fabricante para a conexão correta dos equipamentos.
5. Ajuste da Válvula
Com os instrumentos de medição conectados, inicie o processo de ajuste da válvula. Isso geralmente envolve a abertura e o fechamento da válvula em diferentes posições, enquanto se monitora a pressão e o fluxo. O objetivo é garantir que a válvula responda de maneira adequada às mudanças nas condições de operação.
Durante este processo, é importante registrar os dados obtidos, como as pressões de abertura e fechamento, bem como os valores de fluxo correspondentes. Esses dados serão essenciais para avaliar a precisão da válvula e determinar se ajustes adicionais são necessários.
6. Verificação dos Resultados
Após realizar os ajustes, é hora de verificar os resultados. Compare os dados obtidos durante a calibração com as especificações do fabricante. Se a válvula estiver operando dentro dos parâmetros estabelecidos, a calibração pode ser considerada bem-sucedida. Caso contrário, pode ser necessário realizar ajustes adicionais até que a válvula atinja o desempenho desejado.
7. Desconexão e Reinstalação
Uma vez que a calibração esteja concluída e os resultados verificados, desconecte os instrumentos de medição da válvula. Em seguida, reinstale a válvula no sistema, garantindo que todas as conexões estejam firmes e seguras. É importante seguir as orientações do fabricante para a reinstalação adequada da válvula.
8. Teste Final
Após a reinstalação, realize um teste final para garantir que a válvula esteja funcionando corretamente dentro do sistema. Abra e feche a válvula várias vezes, monitorando o desempenho e verificando se não há vazamentos. Este teste é crucial para assegurar que a calibração foi bem-sucedida e que a válvula está pronta para operação.
9. Documentação
Por fim, é importante documentar todo o processo de calibração. Registre os dados obtidos, os ajustes realizados e quaisquer observações relevantes. Essa documentação pode ser útil para futuras manutenções e calibrações, além de ser um requisito em muitas indústrias para garantir a conformidade com normas e regulamentos.
Se você está em busca de soluções de válvulas de alta qualidade, considere a Válvula spirax sarco , que é reconhecida por sua confiabilidade e desempenho em diversas aplicações industriais.
Em resumo, a calibração de válvulas é um processo que requer atenção aos detalhes e um planejamento cuidadoso. Seguir este passo a passo garantirá que as válvulas operem de maneira eficiente e segura, contribuindo para a eficácia geral dos sistemas industriais. A calibração regular não apenas melhora o desempenho, mas também prolonga a vida útil das válvulas, resultando em uma operação mais econômica e sustentável.
Erros Comuns na Calibração de Válvulas e Como Evitá-los
A calibração de válvulas é um processo crítico para garantir a eficiência e a segurança dos sistemas industriais. No entanto, existem diversos erros que podem ocorrer durante esse procedimento, comprometendo o desempenho das válvulas e, consequentemente, a operação do sistema. Neste artigo, abordaremos os erros mais comuns na calibração de válvulas e forneceremos dicas sobre como evitá-los.
1. Falta de Planejamento Adequado
Um dos erros mais frequentes na calibração de válvulas é a falta de um planejamento adequado. Muitas vezes, os profissionais iniciam o processo sem uma compreensão clara das especificações da válvula ou dos requisitos do sistema. Isso pode levar a ajustes inadequados e a um desempenho insatisfatório.
Para evitar esse erro, é fundamental realizar uma análise prévia das especificações da válvula e do sistema em que ela está inserida. Consulte o manual do fabricante e verifique as recomendações para a calibração. Além disso, elabore um plano detalhado que inclua as etapas do processo, os instrumentos necessários e os parâmetros a serem monitorados.
2. Ignorar a Inspeção Visual
A inspeção visual da válvula antes da calibração é uma etapa crucial que muitas vezes é negligenciada. Ignorar essa etapa pode resultar em problemas não detectados, como desgaste, corrosão ou danos, que podem afetar o desempenho da válvula.
Para evitar esse erro, sempre realize uma inspeção visual detalhada antes de iniciar a calibração. Verifique se há sinais de desgaste nas juntas, selos e outros componentes. Se forem identificados problemas, é recomendável realizar os reparos necessários antes de prosseguir com a calibração.
3. Conexões Incorretas dos Instrumentos de Medição
Outro erro comum é a conexão inadequada dos instrumentos de medição. Conexões soltas ou mal feitas podem resultar em leituras imprecisas, comprometendo a calibração da válvula. Isso pode levar a ajustes inadequados e a um desempenho insatisfatório.
Para evitar esse problema, certifique-se de que todos os instrumentos de medição estejam conectados corretamente e de forma segura. Verifique se não há vazamentos nas conexões e se os instrumentos estão calibrados antes de iniciar o processo. Uma boa prática é realizar um teste inicial para garantir que as leituras estejam corretas.
4. Não Registrar Dados Durante a Calibração
Registrar os dados obtidos durante a calibração é essencial para avaliar o desempenho da válvula e determinar se ajustes adicionais são necessários. No entanto, muitos profissionais esquecem de documentar essas informações, o que pode dificultar a análise posterior e a identificação de problemas.
Para evitar esse erro, mantenha um registro detalhado de todos os dados coletados durante a calibração, incluindo pressões de abertura e fechamento, valores de fluxo e quaisquer ajustes realizados. Essa documentação será valiosa para futuras manutenções e calibrações, além de ajudar a identificar tendências e problemas recorrentes.
5. Ignorar as Condições de Operação
As condições de operação da válvula, como temperatura, pressão e tipo de fluido, podem afetar seu desempenho. Ignorar esses fatores durante a calibração pode resultar em ajustes inadequados e em um funcionamento insatisfatório.
Para evitar esse erro, sempre leve em consideração as condições de operação ao realizar a calibração. Certifique-se de que a válvula esteja calibrada para as condições específicas em que será utilizada. Isso garantirá que a válvula funcione de maneira eficiente e segura em seu ambiente de operação.
6. Não Realizar Testes Finais
Após a calibração, é fundamental realizar testes finais para garantir que a válvula esteja funcionando corretamente dentro do sistema. Muitos profissionais pulam essa etapa, o que pode resultar em problemas não detectados que podem afetar a operação.
Para evitar esse erro, sempre realize um teste final após a calibração. Abra e feche a válvula várias vezes, monitorando o desempenho e verificando se não há vazamentos. Esse teste é crucial para assegurar que a calibração foi bem-sucedida e que a válvula está pronta para operação.
7. Falta de Manutenção Regular
A calibração de válvulas não deve ser vista como uma tarefa única, mas sim como parte de um programa de manutenção contínua. Ignorar a necessidade de calibrações regulares pode levar a um desempenho insatisfatório e a falhas no sistema.
Para evitar esse erro, implemente um programa de manutenção preventiva que inclua a calibração regular das válvulas. Isso não apenas garantirá que as válvulas estejam sempre em condições ideais de funcionamento, mas também permitirá que você identifique e resolva problemas antes que eles afetem a produção.
Além disso, ao considerar a instalação de válvulas, é importante escolher componentes de qualidade, como as Conexões de aço carbono, que são conhecidas por sua durabilidade e resistência em aplicações industriais.
Em resumo, a calibração de válvulas é um processo que requer atenção aos detalhes e um planejamento cuidadoso. Evitar os erros comuns mencionados acima garantirá que as válvulas operem de maneira eficiente e segura, contribuindo para a eficácia geral dos sistemas industriais. A calibração regular não apenas melhora o desempenho, mas também prolonga a vida útil das válvulas, resultando em uma operação mais econômica e sustentável.
Manutenção e Verificação Regular das Válvulas Calibradas
A manutenção e verificação regular das válvulas calibradas são essenciais para garantir a eficiência e a segurança dos sistemas industriais. As válvulas desempenham um papel crucial no controle do fluxo de fluidos, e sua calibração adequada é apenas uma parte do processo. Para assegurar que as válvulas continuem a operar de maneira eficaz ao longo do tempo, é necessário implementar um programa de manutenção que inclua inspeções regulares, ajustes e reparos quando necessário.
1. Importância da Manutenção Regular
A manutenção regular das válvulas é fundamental para evitar falhas inesperadas e garantir que elas funcionem dentro das especificações desejadas. Com o tempo, as válvulas podem sofrer desgaste devido ao uso contínuo, à corrosão e a outros fatores ambientais. Isso pode levar a vazamentos, falhas no controle de fluxo e até mesmo riscos à segurança. Portanto, a manutenção preventiva é uma prática recomendada para prolongar a vida útil das válvulas e minimizar os custos de reparo.
Além disso, a manutenção regular ajuda a identificar problemas antes que se tornem críticos. Inspeções frequentes permitem que os operadores detectem sinais de desgaste, corrosão ou danos, possibilitando a realização de reparos antes que a válvula falhe completamente. Isso não apenas melhora a confiabilidade do sistema, mas também reduz o tempo de inatividade e os custos associados a paradas não programadas.
2. Inspeções Visuais
Uma parte importante da manutenção regular é a realização de inspeções visuais das válvulas. Essas inspeções devem ser realizadas periodicamente e devem incluir a verificação de componentes como juntas, selos e conexões. Durante a inspeção, os operadores devem procurar sinais de vazamentos, corrosão ou danos visíveis.
Além disso, é importante verificar se as válvulas estão funcionando corretamente. Isso pode incluir a abertura e o fechamento manual das válvulas para garantir que elas se movam suavemente e sem obstruções. Se forem identificados problemas durante a inspeção, é recomendável realizar os reparos necessários imediatamente para evitar complicações futuras.
3. Lubrificação e Ajustes
A lubrificação adequada é um aspecto crucial da manutenção das válvulas. Componentes móveis, como hastes e engrenagens, devem ser lubrificados regularmente para garantir um funcionamento suave e eficiente. A falta de lubrificação pode levar ao desgaste prematuro e a falhas mecânicas.
Os operadores devem seguir as recomendações do fabricante em relação ao tipo de lubrificante a ser utilizado e à frequência de aplicação. Além disso, é importante realizar ajustes nas válvulas conforme necessário. Isso pode incluir a calibração de válvulas que apresentem desvios em seu desempenho ou a substituição de componentes desgastados.
4. Testes de Funcionamento
Após a realização de manutenção e ajustes, é fundamental realizar testes de funcionamento para garantir que as válvulas estejam operando corretamente. Isso pode incluir a realização de testes de pressão e fluxo para verificar se as válvulas estão respondendo adequadamente às condições de operação.
Os testes devem ser documentados para referência futura e para garantir que as válvulas estejam dentro das especificações do fabricante. Se forem identificados problemas durante os testes, é importante tomar medidas corretivas imediatamente para evitar falhas no sistema.
5. Registro e Documentação
Manter registros detalhados de todas as atividades de manutenção e verificação é essencial para garantir a conformidade com as normas e regulamentos da indústria. A documentação deve incluir informações sobre as inspeções realizadas, os ajustes feitos, os testes de funcionamento e quaisquer problemas identificados.
Esses registros não apenas ajudam a manter um histórico das atividades de manutenção, mas também podem ser úteis para auditorias e avaliações de desempenho. Além disso, a documentação pode ajudar a identificar tendências e padrões que podem indicar a necessidade de melhorias no processo de manutenção.
6. Treinamento e Capacitação
Para garantir que a manutenção e verificação das válvulas sejam realizadas de maneira eficaz, é fundamental que os operadores e técnicos recebam treinamento adequado. O conhecimento sobre as especificações das válvulas, os procedimentos de manutenção e as melhores práticas é essencial para garantir que as válvulas operem de maneira segura e eficiente.
Investir em treinamento contínuo não apenas melhora a competência da equipe, mas também contribui para a segurança geral do sistema. Profissionais bem treinados são mais propensos a identificar problemas e a realizar manutenções corretivas de forma eficaz.
7. Considerações Finais
A manutenção e verificação regular das válvulas calibradas são essenciais para garantir a eficiência e a segurança dos sistemas industriais. Implementar um programa de manutenção que inclua inspeções visuais, lubrificação, ajustes e testes de funcionamento ajudará a prolongar a vida útil das válvulas e a minimizar os custos de reparo.
Além disso, ao considerar a instalação de válvulas, é importante escolher componentes de qualidade, como a Flange de aço carbono, que são conhecidas por sua durabilidade e resistência em aplicações industriais.
Em resumo, a manutenção regular das válvulas é uma prática essencial que não deve ser negligenciada. Ao seguir as diretrizes mencionadas, as empresas podem garantir que suas válvulas operem de maneira eficiente e segura, contribuindo para a eficácia geral dos sistemas industriais e reduzindo os custos associados a falhas e reparos.
Em conclusão, a calibração de válvulas é um elemento essencial para a operação eficiente e segura de sistemas industriais. Através de um processo bem estruturado, que inclui planejamento, inspeção, ajustes e manutenção regular, é possível garantir que as válvulas funcionem dentro das especificações desejadas. Evitar erros comuns e realizar verificações periódicas não apenas prolonga a vida útil das válvulas, mas também assegura a qualidade do produto final e a segurança do ambiente de trabalho. Portanto, investir na calibração e manutenção adequada das válvulas é uma estratégia inteligente que traz benefícios significativos para a eficiência operacional e a sustentabilidade dos processos industriais.